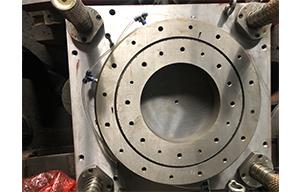
Stator composite mould
The compound mold structure is welcomed by customers because of its high production efficiency and good dimensional accuracy of the workpiece; but also because its convex and concave molds are subject to the constraints of punching, the general processing method is not satisfactory. Therefore, a new type of processing method—corrosion process is presented. The machined parts and components of the generator punching die completely meet the technical requirements.
Stator composite molds: Stator composite molds are generally suitable for 71-180 small stators. Such punches are better to choose. The stator composite mold is better controlled than the concentricity of the stator embossing mold. The stator composite mold is stacked with a relatively smooth finish. The punching die is better, because the die is broken. Generally, the master punching workshop is more difficult to repair and disassemble than the stator punching. It is recommended that the small model is more suitable for the compound die.
When punching the convex position, the mold needs to be lowered to death. You can limit the position between the upper splint planning insert or the pad and the outer plate. The inner and outer stripping forces should be large, and the outer stripping plate should be higher than the convex template for pressing. Cutting edge punching, large convex hull punching needs to be fixed on the plywood, and the punching punch near the convex hull should be planned to be shorter to ensure that the material is pulled and extended before completing the punching action.